In This Article
Share
3D Printing In Architecture
3D printing, architecture, and innovation: Richter collaborates with Intamsys and BASF Forward AM to tackle construction challenges. Solutions include complex components, sustainable materials, and streamlined processes. Richter’s “90-10 Philosophy” guides sustainable project approach.
Solving the challenges in the construction industry with innovative architecture and 3D printing
The week of the 14th of November saw Richter’s 3D printing team collaborate with Intamsys and BASF Forward AM at the Formnext-where ideas take shape 3D printing event.
The theme – solving challenges in the construction industry with innovative architecture and 3D printing – centered around our ability to manufacture complex architectural structures with the help of 3D printed parts for use in numerous high-end architectural projects globally.
Some sample parts were displayed on the Intamsys booth, and we also got the opportunity to present at BASEF’s booth on who Richter is, and our unique but practical approach to solving the challenges faced in the construction industry with innovative architecture and 3D printing.
Our presentation
Globally, over 50% of waste comes from construction and demolition work. Buildings and construction projects are responsible for 40% of greenhouse gas emissions, with the largest share of this emission coming from manufacturing raw material, with packaging and transportation following closely.
As a manufacturing company, we at Richter lighting technologies GmbH are clear with our responsibilities and have been driving our main innovations, towards sustainable development of industrial solutions to meet the challenges of the construction sector.
These challenges are characterized by the following points:
- Reduce the environmental footprint of the construction sector
- Holistic consideration of the materials used over entire product cycle (selection of recyclable materials, reduction of materials used).
- Reduce construction cost and completion times
- Reduce arduous and risky physical labor.
Richter use-cases
As we always put our motto into practice “Richter, where ideas work”, our vision is to enable global clients to create perfect space.
Doing this comes with unique challenges, but we consistently solve for these challenges in numerous high-end architectural projects globally
some examples of projects involved manufacturing custom suspended ceiling and lighting systems for popular retail stores in addition to headquarters and workplaces such as the lobbies of the 50 Hudson Yards building in New York city.
We drew from our expertise in multiple fields, our experience from past projects, and leveraged some of the most innovative technologies to meet clients’ requirements.
3D printing process
We needed to create complex components to combine multiple profiles for architectural structures, and hold our fabrics in the ceiling systems. To achieve this goal, we needed a material with select properties, and a 3D printer that can get the best out of the material.
The material that had the required properties was the ULTEM™ 9085 filament, a polyetherimid (PEI) plasticand the 3D printer used to achieve this task was the Intamsys Funmat pro 610 HT 3D printer.
The printer has a nozzle temperature that goes up to 500 °C adequate for this material because of its high melting point.
It also has a controlled heated chamber, that was set to about 200 °C, which is necessary in order to achieve strong layer bonding for ULTEM™ 9085 filament because of its glass transition temperature of 186° C.
The result was:
- Very complex integrable shapes, that the concept of milling could not even be considered.
- Very durable components with strong layer bonding.
- Lightweight and highly flame-retardant components.
- Reduced materials with infill structure.
Another example is when we had to use the BASF Ultrafuse® PC/ABS FR material.
The major challenge for this project was achieving combination of different materials, assembled as a single piece, and shipped for easy, on-site installation
This component had to have the following requirements:
- Remain invisible
- Excellent surface quality to act as a frame for fabric systems.
- High durability & flame retardant
We achieved this unique architectural component using innovative technologies like (3D printing, 3D engineering, big data analysis, etc.) and the philosophy at Richter Lighting Technologies GmbH.
Richter Approach
For every project we undertake, we follow a unique approach that we developed to bypass the problems clients face during construction.
The Richter “90-10 Philosophy” is a unique approach to construction revolving around four main stages – understanding client needs and requirements, utilizing an extensive library of parts and expertise, conducting most (90%) of the development in-house, and delivering custom solutions that meet agreed requirements.
This process, focused on maintaining clear quality, cost, and lead time, is designed to ensure a sustainable environment across the entire lifecycle of a project. It also ensures that the final product is delivered in a manner that simplifies the installation process for on-site professionals.
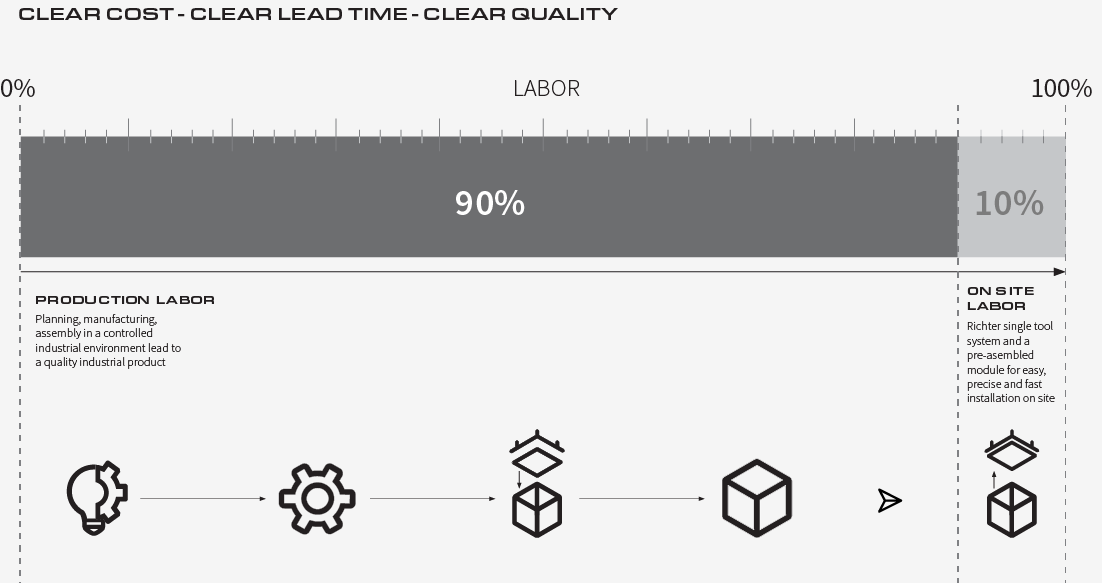